HS2 began work on the high-speed rail project’s pioneering low-carbon Wendover Dean Viaduct, with an expert team of ground engineers sinking the first of almost 63 concrete piles that will form the foundations.
EKFB - a team made up of Eiffage, Kier, Ferrovial Construction and BAM Nuttall – worked with their design partner, ASC (a joint venture between Arcadis, Setec and COWI) and specialist architects Moxon on the ‘double composite’ approach which was inspired by structures on the latest French high speed TGV lines.
Located south of the village of Wendover in Buckinghamshire, the 450m-long viaduct will be the first major railway bridge in the UK to be built with a ‘double composite’ structure, using significantly less carbon-intensive concrete and steel in comparison to a more traditional design.
Over the summer, engineers working for HS2 Ltd’s main works contractor, EKFB will construct 63 concrete piles to form the foundations for the structure.
On top of each group of piles – which will range from between 38 and 46m deep - a concrete pile cap will support the pier which will in turn support the weight of the bridge structure above. Instead of hammering the piles into the ground, holes will be bored before being backfilled to create the pile.
The piers – some of which will be up to 14 metres high – will be cast as shells before being assembled on site and filled with concrete. This approach will reduce the amount of work on site and cut disruption for local residents. The first ‘double composite’ beams will be installed next year.
Andrew Bull, ASC Programme Director, Arcadis said:
“It’s fantastic to see our innovative solutions now becoming reality. I am very proud of our design teams who have worked hard with our client, external stakeholders and the wider supply chain to bring innovation with tangible benefits. This viaduct is a great example of how we can collaborate to achieve win-win-win solutions saving time, money and carbon.”
HS2 Ltd Project Client Rohan Perin said:
“HS2 trains will be zero-carbon from day one, offering a cleaner, greener way to travel, cut the number of cars and lorries on our roads, cut demand for domestic flights, and help the fight against climate change.
“But we’re also serious about reducing the amount of carbon we use during construction, and Wendover Dean is a great example of how we’re using the latest engineering techniques to do just that. Concrete is one of the construction industries’ biggest sources of embedded carbon – and this innovative design will help us cut our carbon footprint while delivering a lighter, stronger and more elegant structure.”
Instead of using solid pre-stressed concrete beams to form the bridge spans, the viaduct will use two steel girders sandwiched between two layers of reinforced concrete to create a super strong but light weight hollow span.
This approach is set to save an estimated 7,433 tonnes of carbon – the equivalent of someone taking 20,500 return flights from London to Edinburgh – and help HS2 achieve its goal of halving the amount of embedded carbon in construction.
EKFB Senior Engineer James Collings said:
“We’re delighted to commence the next stage of construction with the bored piling works. The team has worked hard to deliver the preparatory works ahead of this stage. We’ve also been busy constructing the pier platform for the North side of the viaduct.
“The Wendover Dean Viaduct will sit narrowly between two hills, spanning 450m across, and its design is pioneering, conveying a lightweight structure benefiting from less concrete and steel being used in the construction process.”
As well as cutting the amount of carbon-intensive concrete and steel, the slender design also reduces the silhouette of the structure viewed from across the valley. Nine evenly spaced piers will support the deck of the viaduct and will be placed to carefully reflect the near symmetry of the ground beneath.
The beams themselves will be made from weathering steel, which will age to a characteristically dark russet finish and echo the natural tones of the surrounding landscape.
When viewed from a distance, against the weathered steel, the pale concrete parapet will appear as a thin horizontal band hovering over the slender piers as it glides over the valley and make the whole structure look thinner.
This effect will be further emphasised by the viaduct piers, which have been extended to almost connect with the parapet, helping to give the appearance of a light and narrow structure.
Once construction is complete, the historic field boundaries and hedgerows will be recreated to provide uninterrupted access for farmers and local residents. A mix of trees and shrubs commonly found across the Chiltern chalk hills will be used for new woodland planting around the viaduct, including Oak, Beech, Hazel and Wild Cherry.
ENDS
Wendover Dean Viaduct - Facts and figures
- Location – Buckinghamshire, between South Heath and Wendover. Running north from the Chiltern tunnel, the HS2 route runs along the edge of a shallow valley with the viaduct taking the line over a small side valley.
- Length – 450m
- Maximum height – 20m (Pier 6 is the tallest pier at 14.42m plus the steel and deck will get it to a total height of just under 20m from ground level)
- Design speed – 225mph / 360km/h
- Number of piers – 9 plus 2 abutments (one at either end)
- Spans – 47m
- Designers – HS2 Ltd’s main works contractor EKFB - working with its design partners ASC (a joint venture between Arcadis Setec and COWI) and specialist architects Moxon
- Construction team – EKFB – a team made up of Eiffage, Kier, Ferrovial Construction and BAM Nuttall
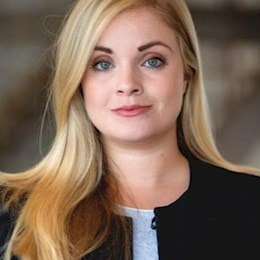